Guide on Custom Wiring Harness
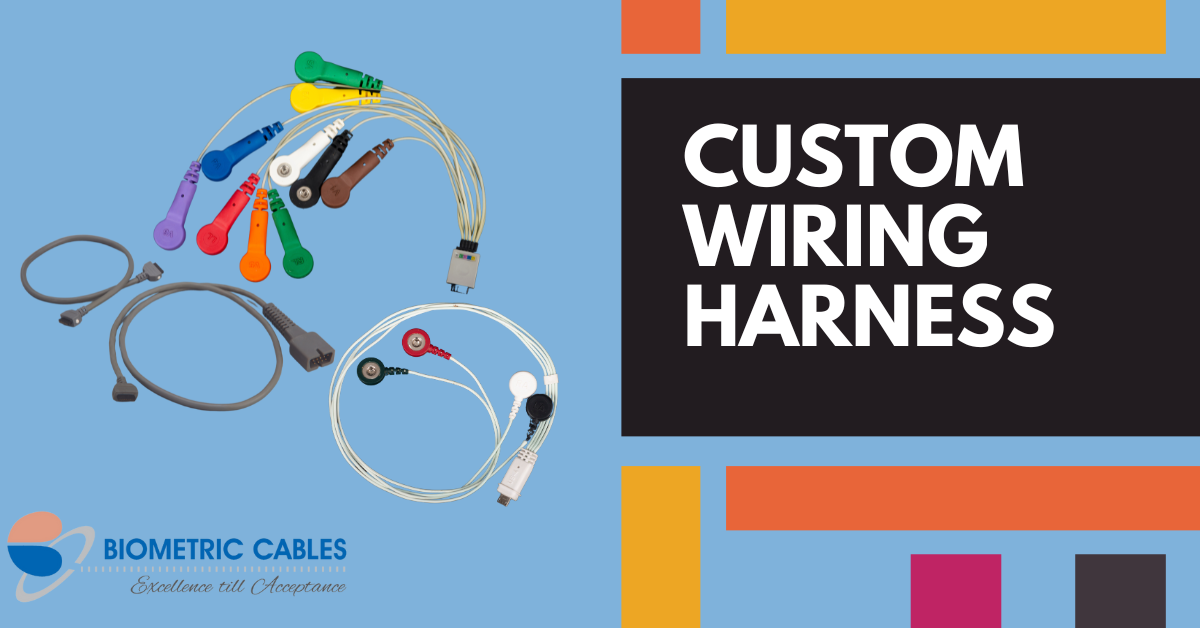
In the fast pace driven medical technological world, reliable connectivity and seamless communication is of paramount importance in bringing forth patient safety, accurate diagnosis and treatment.
What is Custom Wire Harness ?
A custom wire harness also known as wire harness / cable harness. It is a collective assembly of wires, electric components, connectors which forms an unified system. It’s main purpose is to transmit power and electrical signals within the components in the electric devices.
Significance of Custom Wire Harness
1. Installation Process
The custom wire harness offers an efficient and reliable component interconnection, thus simplifying the installation and maintenance process when compared to the usage of single point to point wire.
2. Streamlined Assembly
The assembly process is simplified due to the nature of preconfigured connectors and wires. This inturn avoids the need of complex wiring diagrams.
3. Saves Time and Cost
With conventional point to point wire, the process of cutting , striping , soldering each wire is time consuming and labour intensive. On the other hand, the custom ones emerges as plug and play option, thereby reducing the labour costs and installation time.
4. Minimises space Utilisation
These customised wiring harnesses are specifically designed to minimize space utilisation via organised arrangement of bundled wiring and routing. These comes in handy in areas where there is a limited space.
5. Minimise the Space Utilisation
These customised wiring harnesses are specifically designed to minimize space utilisation via organised arrangement of bundled wiring and routing. These comes in handy in areas where there is a limited space.
The customisation options allows the wire harnesses to precisely fit the unique needs of any applications.The options includes customised colors, lacing , wire ties, custom labelling, Custom shielding etc
6. Incorporation of Customised Options
How are custom wiring harness are designed ?
The design considerations for custom wiring harnesses are as follows
Application specific Requirement Analysis: The wiring harness must align with the intended application’s requirement. Factors such as
Terminal model, specifications
Housing Connector model, specifications
Wire Sheathing / Shielding
Number of wire cores and its specified length
Deciding on the Insulation Materials
Injection Molding / Welding Methods
1. Schematic Diagram:
Schematic diagram / wiring harness diagram refers to blueprint layout on the physical design of a customised wiring harness.It aids in understanding of electrical connections,identification of potential issues,and ensuring the proper routing and wire termination. The schematic design comprises of elements such as Wires, connections, components and electrical symbols.
2. Wire Selection and electrical compatibility:
Depending on the electrical requirements of the application, appropriate wires should be selected carefully based on voltage rating, current carrying capacity, and resistance.Conversely , wrong selection of wires may also lead to insulation breakdown, leading to electrical malfunctions and shocks. The compatibility between connectors,and terminals is one of the essential aspects in attaining seamless connectivity.
3. Selection of connectors:
For reliable and secure connections, selecting the connectors that are compatible with the intended application is of importance.Certain aspects such as ensuring proper locking, connector pin configuration, connector type and mating / unmating mechanisms are of importance.
4. Wiring Routing and Length:
The harness engineers should be able to properly plan and route the wires in a manner that maintains signal integrity and easy installation. Certain factors such as wire length, space constraints,bending radius etc. are crucial in minimizing the interference between the wires and effective wire management.
5. Environmental Considerations:
Environmental factors such as humidity, operating temperature ranges, vibration to be taken into account. To extend the harness durability and longevity, selecting the appropriate materials, and coats are highly essential.
6. Flexibility:
The custom wiring harness designed with future modifications in mind is useful for long term usability and cost effectiveness. The incorporation of additional wires / connectors are beneficial in driving future upgrades.
7. Compliance with Industry Standards:
The customised wire harnesses enables the harness designers to adhere with industry standards and certifications for safety , interoperability and reliability.
8. Custom Wiring Harness Capabilities in Medical :
These wiring harnesses comes with the comprehensive documentation right from the wiring diagram till testing phase. These documentation eases the installation, and traceability processes. On the other hand, Rigorous testing and validation procedures widely ensures the reliability and functionality of the application.The quality and performance of the harnesses can be attained through a couple of testing methods such as continuity testing , resistance testing , tensile strength testing, environmental testing etc. Similarly the importance of manufacturing execution systems can never be overstated as it is essential in monitoring each and every stages such as processes, kpis, staff handling , wire sampling, resources state etc, thus increasing the dependability factor to continuously build which retains the same level of quality as the first.
9. Collaboration with Experienced wire harness manufacturers
Collaborating with experienced harness manufacturers is essential in bringing out the successful implementation of the custom wiring harness projects. They generally possess the expertise and capabilities to design , prototype, manufacture these harnesses according to your requirements.
Depending on the experience of the manufacturer, it is crucial in determining the IPC Certification levels such as Certified Standards Expert (CSE), Certified IPC Trainer (CIT) and Certified IPC Specialist (CIS) that the employees possess.
10. Cost Effective Engineering
Through the implementation of lean manufacturing practices, the workflows are optimised , and the processes are streamlined accordingly. Via waste elimination and efficiency improvements, the cost savings are attained, thus passing to the clients.Investing in a high quality custom wiring harness can ultimately minimise the downtime, the electrical failures risks, and maintenance costs coupled with faulty wires. Through customised wire harness, paying for the necessary feature / functionality helps in eliminating the costs coupled with unnecessary components and features. By purchasing the high quality wire harnesses from experienced manufacturers with proven track record, you could considerably eliminate the upfront costs associated with prototyping, design and engineering.