Wiring Harness Quality Control
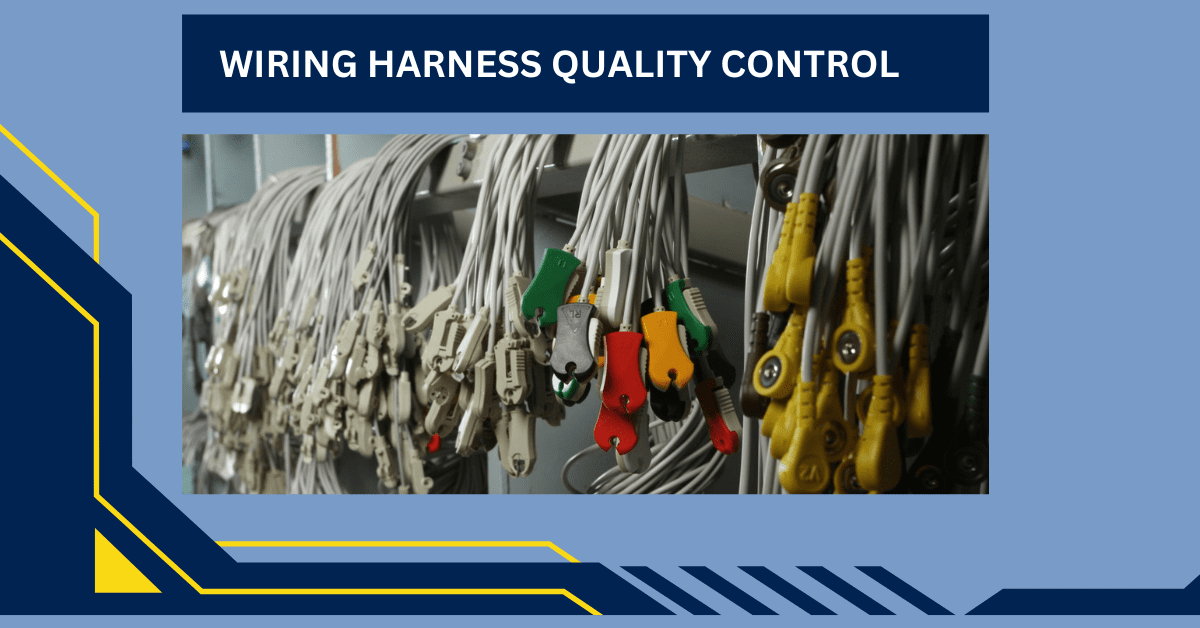
What is Quality in Wiring Harness ?
Components of Wiring Harness Quality Control
Meticulous inspection of raw materials forms the first component of this control. It sets the foundation for the entire proper functioning and reliability of the entire assembly. Sourcing materials from the reputable suppliers and conduction of thorough inspections verifies the compliance with specifications. Secondly, for the proper connectivity of the wiring assembly, the integrity of the connectors and terminals are vital. Proper securing of the connector completely eliminates the wire failures or intermittent connections which possibly can compromise the functionality. A list of comprehensive testing methods and procedures such as environmental testing , insulation resistance testing , wire continuity testing etc is performed to identify the potential issues in each processes.
Continuous Improvement Process
Nowadays, The quality requirements of the medical wire harnesses in the manufacturing process are growing with a lot of complexity and marching towards the zero defect policy. Focusing on the continual improvement in the processes and services drive towards attaining quality medical cables and thereby, continually minimizing the production costs. Continuous improvement processes are incremental cyclical efforts that focus on enhancing the processes, systems and services.
Wiring harness manufacturers who implement continuous improvement processes aimed at driving the following
- Improve Process Efficiency
- Waste Reduction
- Improve the quality
- Minimizes the defects
- Reduction of variations
- Enhance the value delivery
- Cost Savings
- Fosters Innovation
In recent years, Lean manufacturing strategies have gained traction in addressing conventional manufacturing practices. Kaizen is an effective approach that aims at creating perfection through waste elimination and exposes other new areas for improvement. Through establishing the Kaizen methodology, the employees are empowered to provide their own improvements on processes rather than the top-down changes that cause disruption.
Besides, the effectiveness of the lean tools namely 5S ( Sorting, Setting, Shining, Standardising and Sustaining) had engaged the employees in minimizing the waste throughout.
Additionally, the integration of Manufacturing Execution Systems ( MES) with the Kaizen process is instrumental for the success of the continual improvement process such as immediate problem/defect addressing and immediate corrective action.