Wiring Harness Manufacturing Process
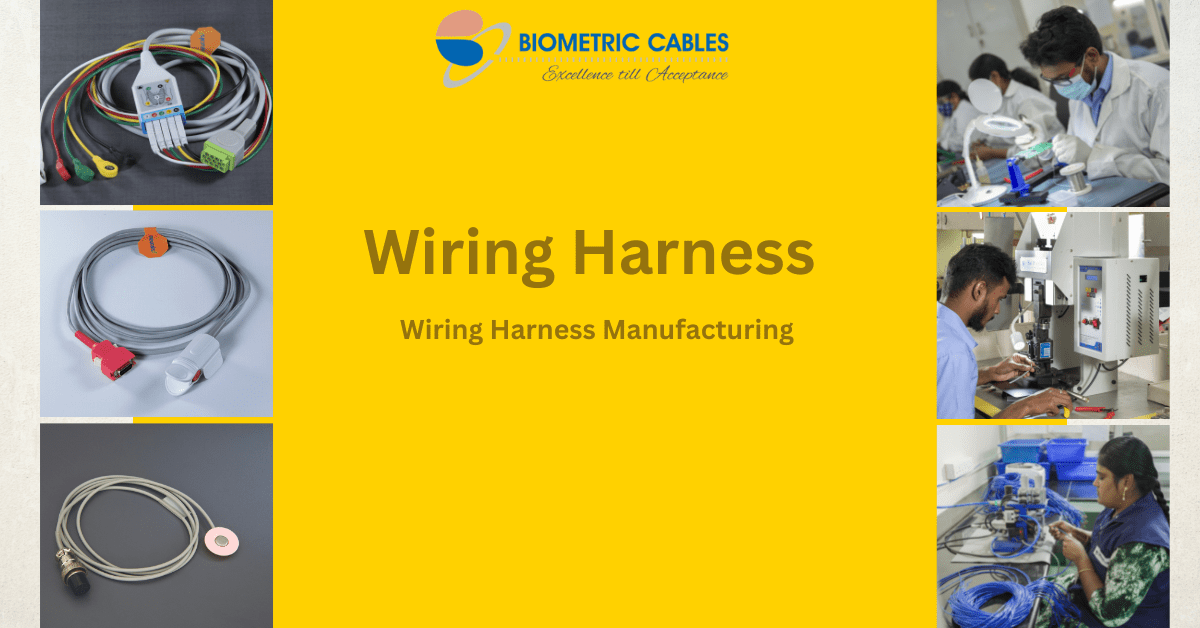
What is Wire Harness ?
Wire harness manufacturing process generally refers to the assembly or group of wires, cables within an insulated material. Usually, wire harness assembly process arrangement begins and ends with a connector type that is intended for its purpose.
The bounding nature of the wire harness assembly process can be attained via sleeving, cable lacing, protective sheathing, strapping etc.In the medical industry, Consistent and reliable performance of the medical equipment greatly impacts patient diagnosis.
Not even the slightest of compromise is tolerated in the performance of medical equipment as it greatly impacts the patient diagnosis. For the effective and safe running of medical equipment and its accessories , rigorous measures have been put into place. The wire harness assembly in the medical equipment is required to pass certified standards and compliance checks.
The knowledge hub throws light on the wire harness manufacturing process :
- Benefits of Wire Harness
- Wire Harness VS Cable Assembly
- Wire harness manufacturing process : How are Wiring Harnesses made ? - Design , Prototyping, Production and Assembly, Testing Phases
- IPC Standard for Wiring Harness
- Customised Wiring Harness
2. Benefits of Wire Harness assembly
Even though transmitting electrical power / signals are of insurmountable purpose in the wiring harness, it certainly reaps other advantages of the harness.
The Wiring harness aids in smooth electrical transmission
A systematic and organized approach of connecting a set of clamped cables and wires to a connector aids in a smoother electrical transmission rather than having various wires connected to different connectors.
Wiring Harness provides well established tight secured and safe connections
Since the wiring harness arrangements are done within the insulated material , it protects the medical equipment from short circuits, abrasions, and moisture.
Wiring harness minimizes the time for the installation process
It simplifies the installation process and minimizes the installation time for the medical equipment applications that requires numerous systems of wiring.
Wiring harness minimizes the clutter
Instead of having lengthy wires scattered over large distances , the wiring harness setup minimizes the clutter , thus making the space ,organized and clutter free.
3. Wire Harness assembly vs Cable Assembly
While both wire harness and cable assemblies terminologies are often misconstrued, in reality, both terms are widely different.
Wire Harnesses
1. The wires and cables are bundled together which are already protected by the outer layer.
2. Ideal for indoor applications such as medical equipment as it provides a minimal layer of protection and it fails to withstand the extreme environmental conditions.
3. Wire harness is a low cost option for an organized bundling of the cables and wires when compared to cable assembly. Even though it is a cost effective and friendly option , it widely depends on the quality, quantity of the wires / cables that are required for mass production of medical equipment and accessories.
Cable Assembly
1.A group of wires / cables braided and wrapped together in a single outer protective sheath which forms an unified approach.
2.Suitable for outdoor applications as it withstands major extreme conditions.
4.Pre-Production, Production and Post Production processes (How are wiring harnesses made?)
1. Wiring Harness Process Assembly :Preproduction
Design: Begins with Wiring Harness Diagrams
Wiring harness diagrams ( also commonly known as circuit diagrams/ schematics ) form the foundational basis for the custom wiring harness assembly.The wiring harness diagram represents the physical layout of the wire connections and their associated components. Several software models such as AutoCAD aids in the wiring diagrams. Depending upon the electrical and geometric requirements of your medical device, the wire harness is designed for it’s intended purpose.
Factors to be considered while selecting the appropriate components for wire harness design
The Selection of the right components widely influences the wire harness performance for the medical application.
Is it intended for medical applications in extreme working conditions or indoor hospital spaces?
Will the wire harness be exposed to hazardous chemicals, corrosive fluids, fumes?
Exposure to continuous flexing or static in nature ?
Factors such as minimum, and maximum operating temperature conditions
Selection of the appropriate wires based on the number of circuits, number and types of conductors, platings etc
The required operating voltage level
3. Wiring Harness Manufacturing Process: Production Stage
The processes involved in wiring harness are a combination of hand (manual )assembly, automation and semi-automation.
Wire Cutting
The first and foremost step is the process of cutting the wires required for the medical equipment design. The wires that are required are cut according to the specific length using the cutting machine.
Cutting and Stripping Process
Layout
Once the wire cutting is done, the assembler keeps the wires organised and intact with the help of straps/cable ties.
Wire Stripping
Secondarily, the automated stripping machines ease the task of stripping the insulation of the wires where the wire’s metal is exposed that are ready for the crimping process.
Stripping Process
Stripping the fine cores
Wire Crimping
With the aid of handheld/automated crimpers, Crimping the terminals on the ends of the wires are performed and the wires are fitted into the connector.
In wiring harness assembly, usually Crimping surpasses the Soldering procedure.
Crimped wire harnesses are basically more effective than soldered wire harnesses as they shield against intruding dirt debris and moisture. On the other hand, it also provides consistent connections between the wires / cables rather than a soldered wire harness.Crimping processes can be automated or semi-automated.
Wire Soldering
Even though Soldering is a traditional option for terminating wires, they find the benefits of being affordable as it involves only minimal tools and materials such as flux, solder. Soldering the wire terminations is one of the processes which can benefit via automation( solder machine).
Welding
Ultrasonic welding is regarded as one of the essential joining technologies employed in wiring harness manufacturing. This low-resistance welding process suits applications that involve the usage of smaller wires. For instance, the ultrasonic welding of the wires is carried on in our ESU accessories such as cautery pencils).
Ultrasonic Welding
A Certified wiring harness manufacturer performs quality control and assurance checks at each stage of the processes.
4. Wiring Harness Testing: Post-Production Stage
Lastly, the wiring harness assembly is tested using the help of the programmable wiring harness tester. The bunch of wiring harness are connected to the tester to
Check on the electrical functionality
To identify the faulty wiring harness
Demonstrates compliance with the quality standards
5. IPC Standard for Wiring Harnesses
The IPC / WHMA A 620 D standard proposes the cable/wiring harness manufacturing requirements and practices. IPC / WHMA A 620 D quality standard outlines the practices , techniques, materials, tests and acceptance criteria for the production of crimped, mechanically secured and soldered interconnections in the cable/ wiring harness assembly. Selection of the right manufacturer with vast knowledge and expertise who conforms to the industry consensus standard contributes to a quality medical device.
6. Customised Wiring Harness
While associating with a certified wiring harness manufacturer, it is certainly essential to check on manufacturers who offer customized wiring harnesses based on your medical equipment application and requirement. To have an ideal quality and reliable medical device designed using a wiring harness, working consistently with your certified , customized wiring harness manufacturer is certainly of paramount importance.
Wiring harness assembly can be a custom-made with variety of options such as customised colors, custom shielding , four color ink stamping etc